To be a world-class component supplier, Otter requires to maintain highest consistency in quality and supply, every time.
Otter Controls India: An Indo-British joint venture, delivers high-quality engineering products and services to automotive and non-automotive sectors in India and globally. The company operates a lean manufacturing facility and continuously drives improvements using proven manufacturing techniques.
Three BIG Problems that held them back!
With every advancement in electronic components, circuit geometry kept evolving.
As an EMS part manufacturer, each new product demands an entirely new manufacturing approach, potting material, and component geometry.
For Otter, the challenge was handling a critical material that required precise potting at a small mixing ratio of 100:8 and a shot size of just 4 gm.
The BIG Question
How do you ensure reliable, precise potting for advanced electronic components with fast-changing geometries and challenging materials?
Limited Options: Available potting machines lacked flexibility and precision. Importing a potting machine was not only 3x to 4x costly, but offered very limited flexibility, delivery possible only in 6-8 months and higher risks in implementation.
Otter required a complete potting solution.
In small quantities dispensing, integration of the mixing unit with the right dispensing automation is very critical to achieve 100% accuracy. Twin designed an complete solution. The deciflow dispening technology from Twin is proven for quantities as small as 0.4 g.
Fixtures, programs, workstation complete with X-Y Robot - Twin developed a total solution for Otter. And one that could be easily configured for any future changes in component geometry, dispensing shot or material changes.
All in less than 16 weeks. Can’t beat that 🙂
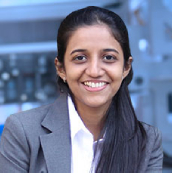
Sanchita Bhalwankar
Expert in Potting Solutions'
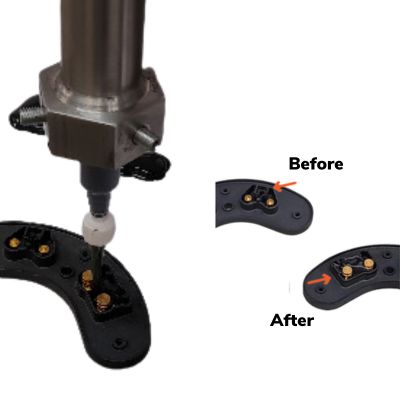
Component Specification
- Epoxy
- Ratio of 100:8
- Shot size of 4 gm
- Process: Atmospheric Potting
Benefit from Twin's advanced mixing and dispensing technology
First time right component
Zero errors in potting
Near-zero rejection rate
NO RISK if component changes
NO Operator dependency
Getting the total solution from Twin made things really easy for us! After implementation, we realised how much time we could have spent if we were to get this done from multiple suppliers or do it with trial and errors at our end.